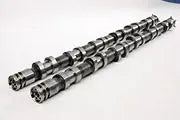
International Customers:
Click Here | Contact Us
Our cams are designed to produce more power by harnessing more residual exhaust gas heat, pressure and velocity to impart greater motion to the turbine, which helps develop turbo boost pressure more efficiently. On the inlet side, careful matching of the valve opening and closing valve events to the piston motion of the long stroke (1.55 L/R ratio) provides much greater cylinder filling capacity, hence engines develop considerably more power from a given boost level.
All lobe profiles are inverted flank asymmetrical designs, with a faster rate of lift to allow the passage of intake/exhaust gases more efficiently. The actual valve lift is only increased slightly to maintain valvetrain stability at high RPM. We also reduce the base circle dimensions slightly to reduce lifter preload, thereby allowing the lifter to function correctly. Due to factory machining variations in the cylinder head, all lifter preloads must be checked when installing cams to ensure preloads are within minimum and maximum tolerance.
The unique feature of our inlet lobe designs is our 'Duo phased' timing; a split lobe centreline opens one inlet valve before the other, introducing swirl into the combustion chamber. This increases the effective duration of the inlet without changing manifold vacuum. We developed this innovation in 2006 and it is interesting to note that Ford has also since introduced swirl technology into the FG engine in 2008.
Ford Barra DOHC Engines